Transportation
Management System
Plan, track and optimize the logistics deliveries with
advance cloud based scalable software.
CLIENT INTRO
Who we are ?
Agro Tech Foods Ltd (ATFL) is the Indian subsidiary of Conagra Brands, Inc. of USA, one of the world’s largest food companies. ATFL manufactures a wide variety of food products and edible oils including Act II popcorn, Sundrop oats, Sundrop peanut butter, and Sundrop cooking oils. AT foods is a publicly listed company with a presence on both the National Stock Exchange (NSE) and Bombay Stock Exchange (BSE). As of March 2023, AT foods reported an annual revenue of 849.7 crore INR.
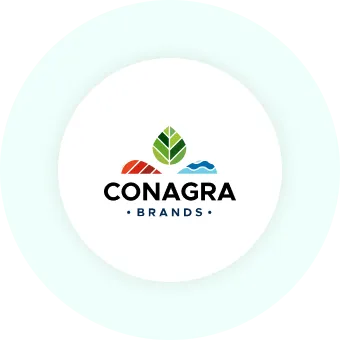
Business Challenge
The approach that riddled with multiple inefficiencies

Ineffective operations
Manual handling of the supply chain was a laborious and time-consuming process. Despite the best efforts of factory managers, the lack of adequate tracking mechanisms led to inexplicable supply chain inefficiencies. Managers also had difficulty with holding the transport operators accountable. In short, manual supply chain management was an ineffective process that simply had to be replaced.
Quality control issues
Tracking the quality and quantity of shipped goods manually was a time-consuming process that required extensive documentation. The team had difficulty determining if every necessary quality check had been carried out for the delivered shipment. This led to quality control issues and poor production output.
Production delays
Inefficient supply chain operations also meant that shipments routinely arrived late. This contributed to production delays and loss of market opportunities.
Lack of visibility
Traditionally, the supply chain efficiency was at the mercy of the transport operators. AT Foods had little control over tracking shipments, ensuring timely loading, delivery, and unloading. This lack of visibility contributed to chaotic operations and an ineffective supply chain.
Revenue loss
Since AT foods was dealing with perishable raw materials, delivery delays could potentially destroy an entire shipment. This resulted in significant revenue loss to the company.
Employee dissatisfaction
A lack of control and the high stakes involved contributed to employee stress and dissatisfaction. Factory managers, in particular, faced significant stress coordinating supply chain activities. The result was reduced employee morale and hampered productivity.
Negative Brand Image
Loss of revenue and opportunities due to an inefficient supply chain caused a loss of trust among distributors and negatively impacted the brand image.
To address these shortcomings and keep up with its growth AT Foods required a logistics solution that could streamline its supply chain operations.
Technologies
Our Specialized Technology Toolkit
Solution
Cloudesign delivered end-to-end logistics digitization capabilitiesthat completely transformed AT Foods’ supply chain.

Indent Planning
A fully-featured indent planning module allowed the factory manager to plan every trip in detail. The module captured details like source, destination, travel route, and trip start time. Indent planning packed advanced features like route planning and load optimization that used sophisticated algorithms to plan cost-efficient trips.
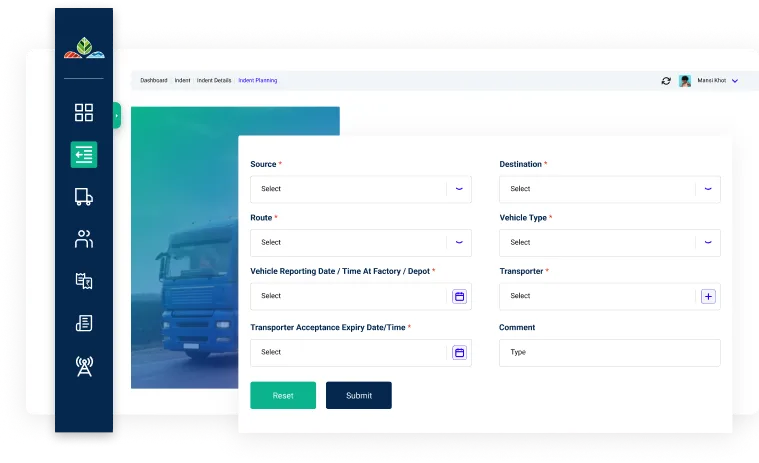
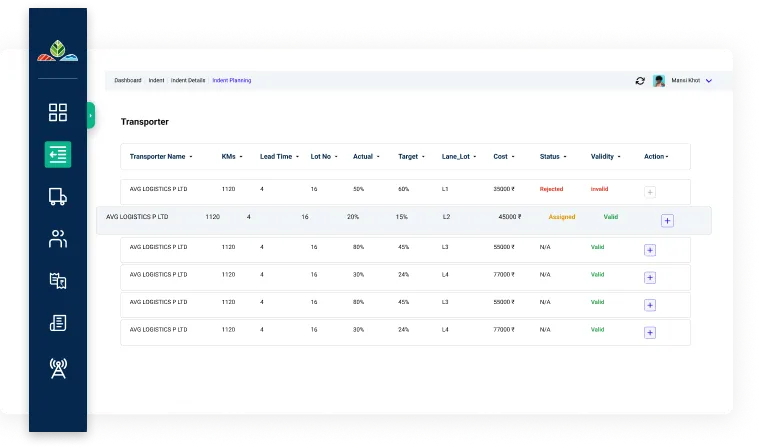
Transporter Bidding
With Cloudtrack, AT Foods could onboard all the transporters they worked with onto a single platform. After the initial planning of a trip, the trip was opened up to transporter bidding. Different transport service providers could then browse through the trip details and bid for the contract in real time. Factory managers could now pick the most cost-efficient transporter at the click of a button. The most suitable bid was finalized and the rest were marked as rejected/expired.
Trip Creation
Post indent planning and successful transporter bidding, a trip was created complete with details like trip number, transporter details, route, vehicle number, driver details, and driver phone number. At this stage, the trip status was still marked as ‘planned’.
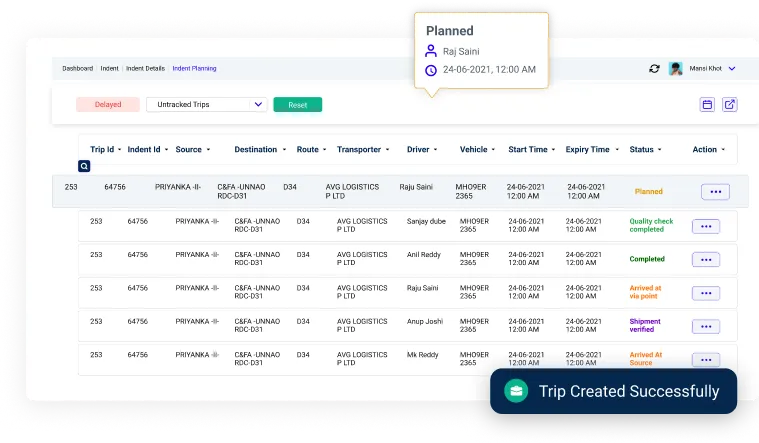
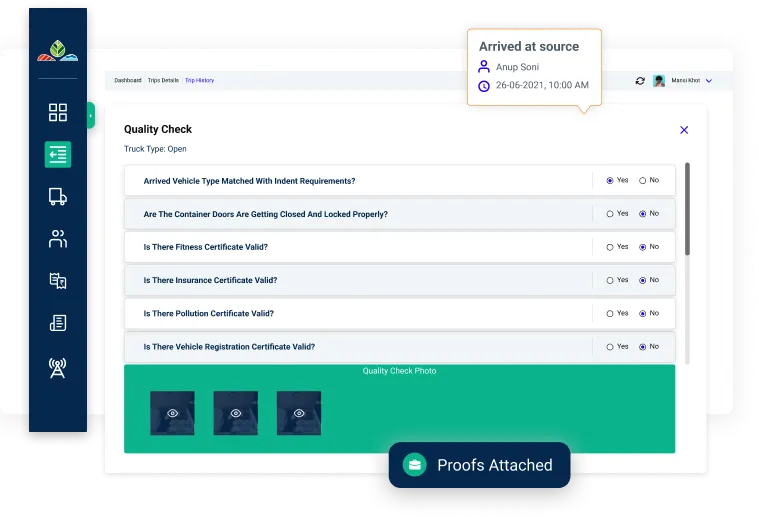
Quality Check
This stage commenced once the transporter vehicle arrived at the loading point. The trip status now changed to ‘Arrived at Source’. Comprehensive quality check of the vehicle was carried out to ensure shipment safety. Checks were carried out for driving license validity, fitness certificate, insurance, pollution certificate, registration, condition, and more. The goal of this stage was to ensure the vehicle was fit for loading edible products. A comprehensive digital report was created and attached to the trip.
Loading
Post the quality check, goods were loaded onto the vehicle. The trip status now changed to ‘loading’. Loading was carried out in accordance with the optimized loading plan generated digitally. Factory managers received real-time notifications of the loading process.
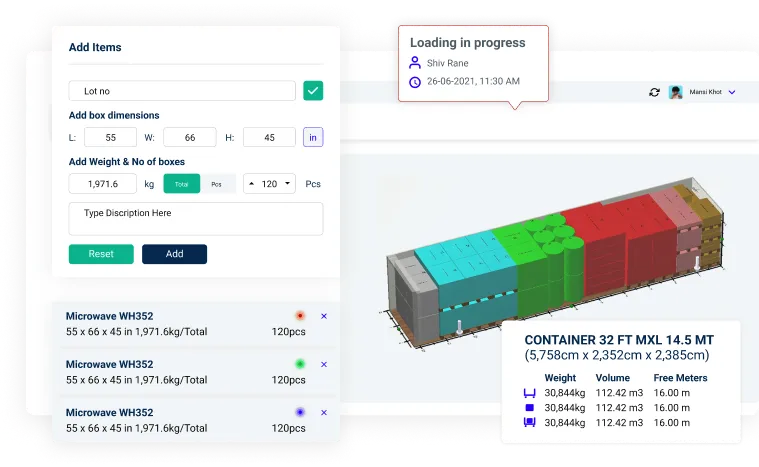
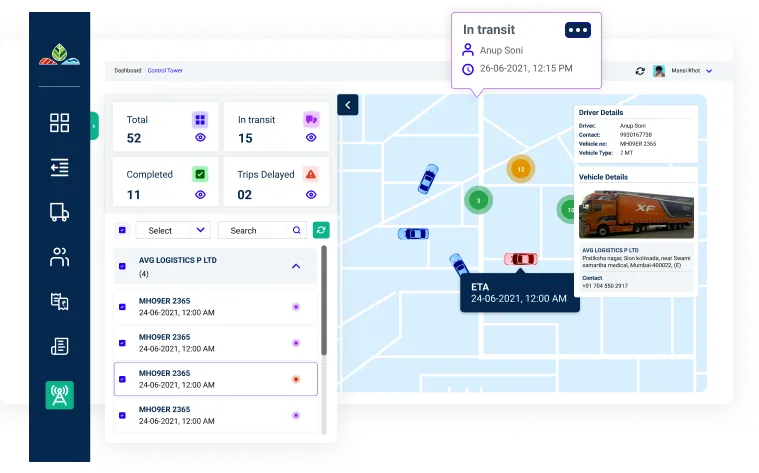
Tracking
Post successful loading, the trip commenced. The status of the trip was now set to ‘In Transit’. Through fool-proof GPS tracking, factory managers could now monitor the status of the trip, the route being taken, the distance covered, and the estimated time of arrival. A special digital module called ‘Control tower’ provided an intuitive GUI map interface through which all the trips in transit could be visualized.
Unloading
Once the shipment reached the final destination, the unloading process began. Intermediate shipment stopping points were reflected on the platform with the tag ‘Arrived at via point’. At the final destination, quality checks were carried out to ensure the shipment was not damaged during transit.
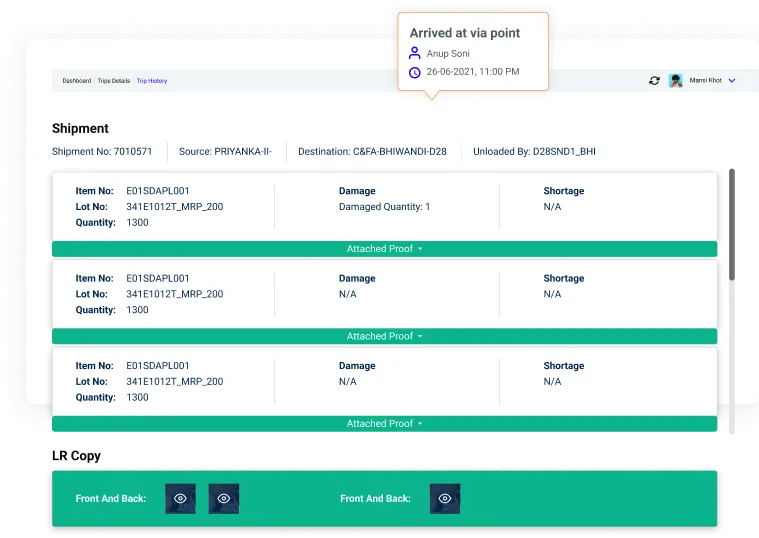
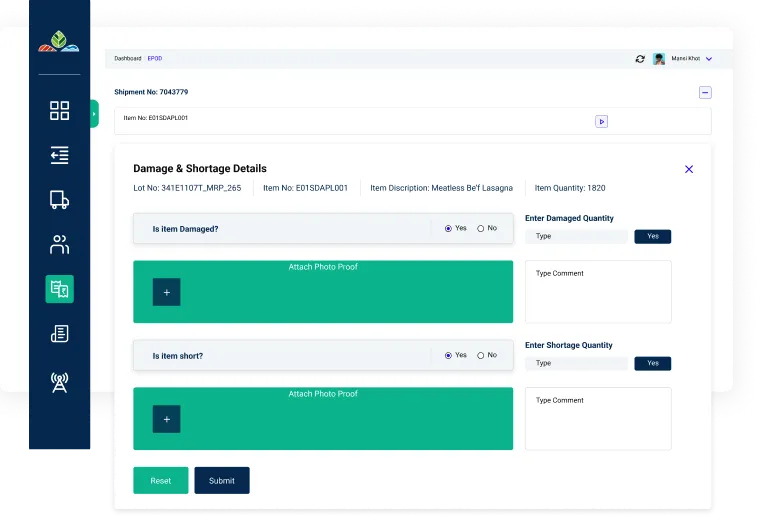
Proof of Delivery
Post comprehensive quality checks, an Electronic Proof of Delivery (EPOD) was created if the delivery was satisfactory. In case of any discrepancies, the trip was marked as rejected.
Billing
Finally, the trip was marked as completed post successful delivery. The invoice was generated and payments were made to the supplier and transporter.
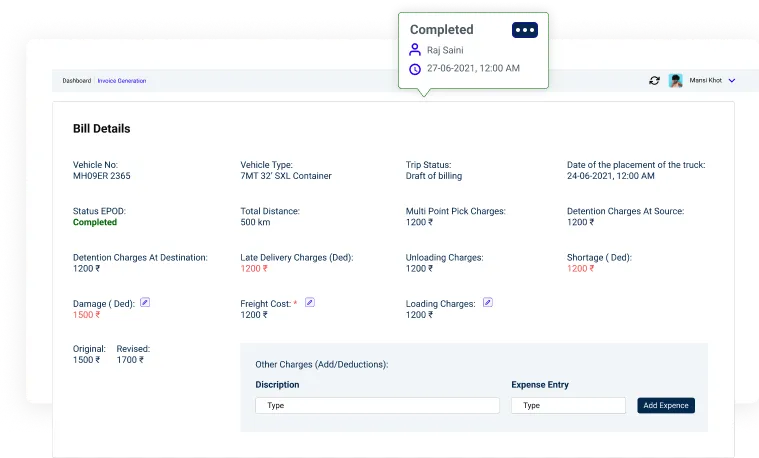
features
Apart from a detailed trip lifecycle module, Cloudtrack also featured convenient technical features like
Role-based Access
The platform provided secure logins and access control based on roles like factory manager, transporter, driver, and supplier. All these roles could collaborate seamlessly on the platform for a successful trip execution.
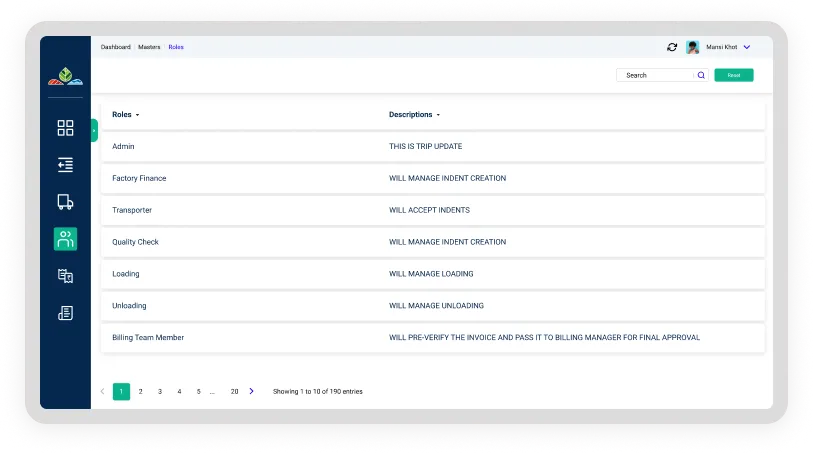
Benefits
A state-of-the-art logistics management system bestowed many benefits upon AT Foods.
Some key benefits that Cloudtrack created included
37%
Shorter Operational Turnaround Time
12%
in Cost Savings
20%
increase in Revenue
Improved
employee morale
Improved brand perception
among distributors and clients
Drop us a line
Lets Collaborate
ClouDesign Your Digital Ecosystems to Drive Peak Organizational Performance
Your First Consultation is Free!
Send us an email at
sales@cloudesign.com